Copper Forgings
Cerro Fabricated Product’s niche for forging copper parts is low to midsize volumes for parts weighing up to 30 lbs., depending on the geometry of the part.
Copper forgings offer a number of advantages over other manufacturing processes. Forging adds superior mechanical and physical properties created by heat and pressure, for example. Products manufactured from forged copper are able to withstand high temperatures and higher loads than other materials. They also perform well in high stress applications with lower failure rates than other materials. There is no porosity in the forging process.
Copper forging is a popular industrial application because of its electrical conductivity, malleability, heat, ductility, machinability, and wear resistance.
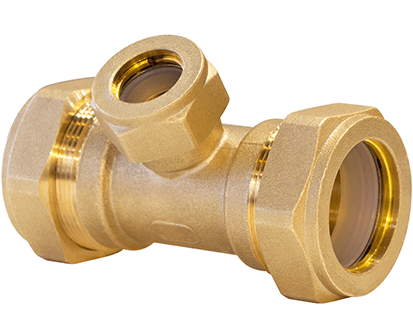
Applications
Forged copper is widely used in the following fields:
- Aerospace
- Chemical Industry
- Automotive
- Petroleum
- Communications
- Electronics including consumer electronics.
Products manufactured using copper alloys include:
- Electronic components / electrical connectors
- High temperature equipment fittings
- Refrigeration equipment
- Power plant applications
- Pump and valve components for high wear and corrosive environments
- Seals and gaskets for high-wear, high-temperature, and corrosive environments
- Connectors, fittings, and caps
Copper Forging Industries
While copper forging has established its significance across various sectors, specific industries and applications stand out. Aerospace, automotive, electrical, and plumbing heavily rely on copper forgings. Given copper’s electrical conductivity, forged copper components are integral in electrical transmission systems, circuit breakers, and electrical contacts. Additionally, the automotive industry uses copper forgings for components that require high strength, excellent conductivity, and resistance to corrosion, such as bushings, bearings, and gears.
Benefits of Using Forged Copper
- Durability: Forged copper parts are known for their remarkable durability, thanks to the forging process which refines the grain structure and improves physical properties.
- Corrosion Resistance: Copper inherently resists various forms of corrosion, ensuring that the components maintain their structural and functional integrity over extended periods.
- Aesthetic Appeal: Copper parts often have a pleasing visual appeal, especially when polished, making them suitable for applications where aesthetics matter, such as in architectural components.
- Eco-friendly: Copper is recyclable, making components manufactured from it eco-friendly. This recyclability ensures a reduced carbon footprint when compared to components made from non-recyclable materials.
Understanding the Copper Forging Process
The process of copper forging involves heating the metal until it’s malleable and then applying force to shape it into the desired form. Various factors play a role in determining the properties and quality of the forged product:
- Temperature: The forging temperature should be precisely controlled. Too high, and the copper may become too soft or even melt. Too low, and it might not achieve the required malleability.
- Rate of Cooling: The rate at which the forged part is cooled can affect its final properties. Rapid cooling, for example, can increase hardness.
- Die Design: The design of the forging die determines the shape, precision, and quality of the finished product. Skilled die design ensures uniformity and minimizes defects.
- Finishing Processes: After forging, the copper part may undergo various finishing processes like machining, grinding, or polishing to achieve the desired dimensions, surface finish, and aesthetic appeal.